Tracer Gas Leak Tester (Helium or Hydrogen Leak Tester)

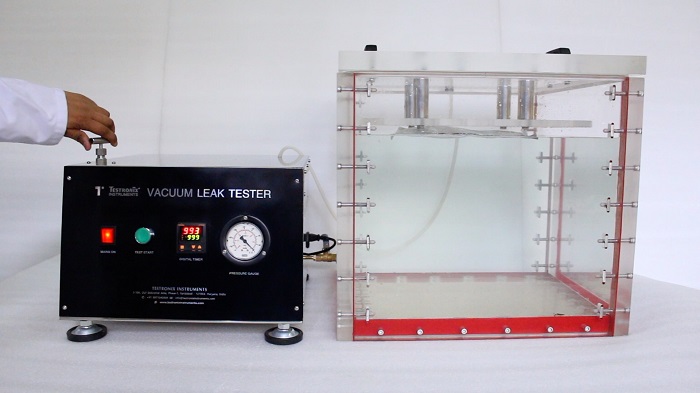
Used in: Aerospace, automotive, electronics, and semiconductor manufacturing
Associated Industry Standards:
- ISO 20485 (for tracer gas leak testing)
- ASTM E493 (for bubble emission techniques)
Specifications:
- Uses helium or hydrogen as tracer gases
- Highly sensitive, can detect very small leaks
- Ideal for high-precision applications
- Suitable for complex geometries and hard-to-reach areas
Pressure Decay Leak Tester

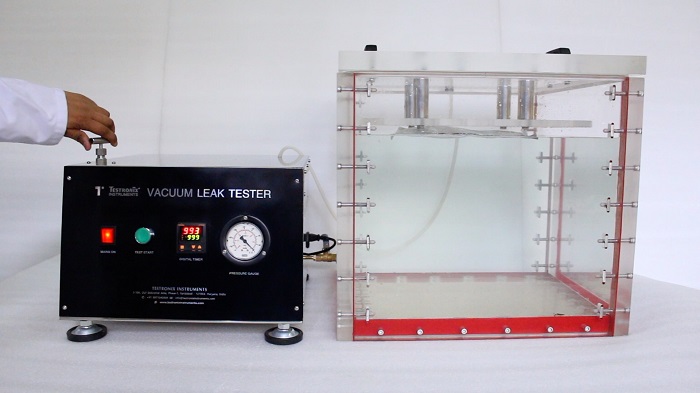
Pressure Decay Leak Tester
Used in: Automotive, HVAC, plumbing, manufacturing (pressurized systems)
Associated Industry Standards:
- ISO 9001 (general quality management)
- ASTM D4991 (for pressure decay leak testing)
Specifications:
- Uses pressure application to detect leaks
- Ideal for pressurized systems like pipes, tanks, and valves
- Quick results with high reliability
- Detects both small and large leaks
Bubble Emission Leak Tester

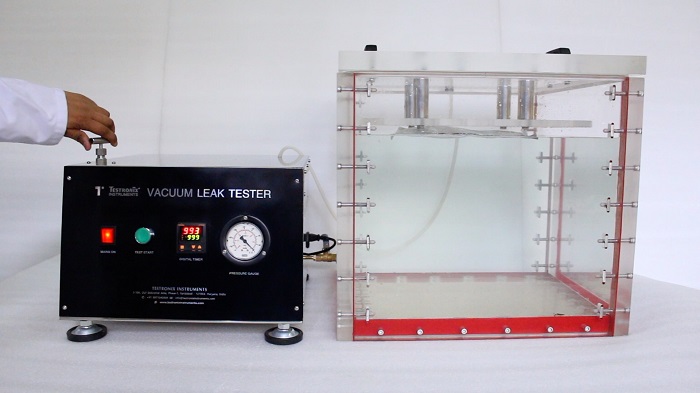
Used in: Food packaging, general consumer goods, simple applications
Associated Industry Standards:
- ASTM D3078 (for flexible packaging)
Specifications:
- Simple and cost-effective
- Suitable for large leaks
- Easy to use and quick results
- Requires water submersion or a soap solution to detect leaks
Mass Spectrometer Leak Tester

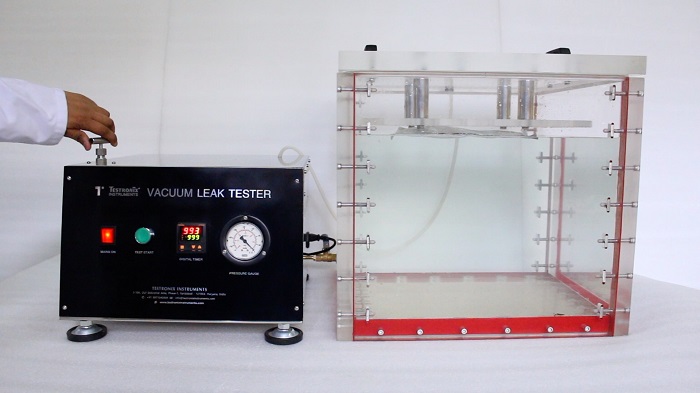
Used in: Aerospace, semiconductor manufacturing, automotive, high-precision electronics, vacuum systems, medical devices
Associated Industry Standards:
- ISO 20485 (for leak testing using tracer gases)
- ASTM E493 (general leak testing methods including mass spectrometry)
- ASTM F2338 (for medical and pharmaceutical packaging)
Specifications:
- Detects even the smallest leaks down to the molecular level
- Real-time measurements
- Capable of handling complex geometries
- Versatile gas leak detections
Dry Vacuum Leak Tester

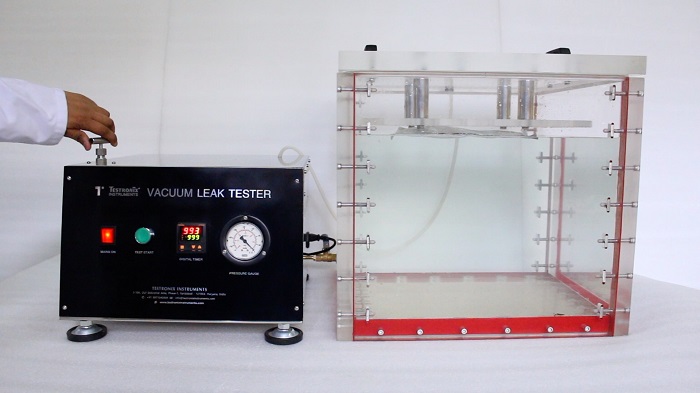
Used in: Electronics manufacturing, pharmaceutical packaging, medical devices, food and beverage packaging, automotive components
Associated Industry Standards:
- ASTM D3078 (Standard Test Method for Determination of Leaks in Flexible Packaging by Bubble Emission, adapted for dry methods)
- ASTM F2338 (Non-Destructive Detection of Leaks in Packaging)
- ISO 11607 (Packaging for terminally sterilized medical devices)
Specifications:
- Detects leaks through precise vacuum pressure measurements, without using liquids
- Non-destructive testing suitable for products sensitive to moisture exposure
- Measures even minor pressure drops for high-accuracy detection
- User-friendly interface with automated test cycles
- Customizable for various product sizes and shapes, including rigid and flexible packaging
What is Common Standards for Vacuum Leak Tester

To ensure product integrity and industry standards, Testronix follows all national and international standards for vacuum leak testing machines. These standards are widely followed by industries all over the world that guarantee product safety, efficiency, and performance. Let’s have a look at them
- ASTM E2377 – Standard Guide for Vacuum Leak Testing
- ISO 14457 – Packaging—Leak Testing using Vacuum Decay
- ASTM D3078 –Standard Test Method for Leak Testing of Flexible Packaging by Internal Pressurization (Bubble Test)
- ASTM F2338 – Standard Test Method for Non-destructive Detection of Leaks in Packaging Using Vacuum or Pressure Decay
- MIL-STD-883 Method 1014 – Microelectronic Devices: Leak Testing
- ISO 9001 – Quality Management Systems
- ASTM F2096 – Standard Guide for Leak Testing of Packaging
- ASTM F3036 – Standard Guide for Leak Testing of Medical Devices
- F3169-16 – Standard Test Method for Leak Detection in Blister Packaging
- F3039-23 – Standard Test Method for Detecting Leaks in Nonporous Packaging
Testronix is a leading manufacturer and supplier of vacuum leak testing equipment and offers cutting-edge solutions for leak detection. For highly efficient and cost-effective vacuum leak testers, get a quote from Testronix Instruments.
What are the Typical Components of Vacuum Leak Tester?

A vacuum test equipment contains several key components contributing to the detection of leaks in sealed products. These include the vacuum chamber, vacuum pump, pressure sensors, control system, display unit, test piece fixtures, and valves. Each of these components plays a critical role during the testing process creating a vacuum environment for determining the test results. Here is a detailed explanation of all components –
Vacuum Chamber
This is the container where the sample is placed during leak testing. It is supposed to hold the object in place while exposing it to the vacuum pressure inside. During the testing, it ensures the prevention of any external air.
Vacuum Pump
The vacuum pump is a critical component of the vacuum leak test apparatus which is responsible for creating and maintaining the vacuum inside the chamber. It draws air out of the chamber to create the low-pressure environment needed for leak testing.
Test Piece Fixtures
The purpose of these fixtures is to securely fasten the product under test within the vacuum chamber. They ensure that the sample is properly sealed so that variations in pressure can be measured precisely.
Pressure Sensors
A pump is essential in leak testing as it provides the vacuum inside the chamber. This pump will suck air out of the chamber to create the low-pressure requirement for leak testing.
Control System
This is the central processing unit of a vacuum leak tester, responsible for processing the series of operations. It deals with the control of the vacuum pump operation and controlling sensor readings that are then processed to determine if a leak exists or not.
Display Unit
The display unit shows the result of the leakage test in real-time. Normally, it contains information about changes in pressure, details concerning the test times, and whether the product passed or failed the test.
Valves
Valves control the flow of air into and out of the vacuum chamber. They help maintain the correct vacuum levels and allow the tester to return the chamber to normal atmospheric pressure after testing.
How Does Vacuum Leak Tester Work?

A Vacuum Leakage tester detects leaks in sealed products or packages by determining variations in pressure within a vacuum. This is essentially based on the fact that if there's a leak, the sealed object will decay at a different rate concerning the internal pressure, whereas the perfectly sealed item will not have any deviation.
Working Principle
The mechanism behind a vacuum leak testing equipment relies on pressure differential. Once sealed inside the vacuum chamber, the tester removes air in the chamber by creating a low-pressure environment around the product. Nothing happens if the product is airtight. However, the pressure difference would force air or gas through the leak into the vacuum surrounding the product if any leakage were present.
The escaping flow of air or gas is sensed by sensors within the chamber, which can measure either pressure variations or flow rates. This helps in leak detection since even the minute leak is easily detectable. The pressure is low, which extends the flow of air pressure outside through defects, making this a highly sensitive and reliable leak test.
Step-by-step process of how vacuum test machine works –

Creating a Vacuum
The test begins by placing the object under test into the vacuum chamber. This procedure causes a vacuum due to the vacuum pump operation, which removes air from the chamber, thus setting a low-pressure environment. This step in the test is very important since the pressure drop will enable easy leak detection.
Monitoring Pressure Decay
Once this vacuum level in the chamber has been achieved, the pressure inside that chamber is monitored by pressure sensors. If the object tested is sealed leak-tight, then the pressure inside the chamber should not change. But if there were a leak in the object, air would gradually leak into the object, causing the pressure to rise; this pressure decay is measured and analyzed.
Leak Detection
The pressure change is continuously sensed by the control system. If the rate of pressure leakage is more than a predetermined value, then surely there is a leak. The system will give an alarm or mark the product as bad. The higher the leakage, the greater will be the rate of pressure change. The tester can be dialed to measure the different sizes of leaks according to the sensitivity required.
Returning to Normal Pressure
After the completion of the test, vacuum sealing within the system opens valves to release the vacuum and recapture atmospheric pressure within the chamber. The testing specimen is removed from the chamber, and the test results are displayed on the control unit that notifies whether the product passed or failed the leak test.
Vacuum Leak Tester Application and Real-life Examples

A vacuum leak tester or vacuum testing machine is an essential tool for those sectors where leak-tight seals, packaging, or constituents are of extreme importance. It helps to test for leaks in a product by measuring the pressure decay in a vacuum environment.
Packaging Industry
The packaged product is sealed properly in a manner that air, moisture, and other contaminants have not penetrated the package.
Example – Chips and snacks and vacuum-wrapped meat in the food packaging sector require tight packaging to enable long preservation time and freshness. Vacuum leak testing is applied to make sure that there are no tiny holes or leaks in the package that could easily trigger spoilage.
Pharmaceutical Industry
This testing confirms that the drug and medical product are in sealed and sterile vacuum conditions.
Example – Temperature-sensitive drugs like vaccines are packed in evacuated sealed containers. The vacuum leak tester for bottles ensures the seal is tight and won't create any opportunity for contamination to compromise the efficacy of the drug.
Medical Industry
In the medical industry, the sterility of medical devices and the packaging they come in can range from syringes and IV bags to surgical instruments.
Example – Syringes and surgical instruments require a hermetically sealed package to preserve the sterility of the instrument. A vacuum testing machine ensures that the package for those products is sound, with no pinhole-sized leaks that would allow air to pass through, compromising sterility or safety.
Automotive Industry
Seal leak testing on auto parts, so they seal perfectly and serve their intended purposes.
Example – Most car parts need tight seals, such as fuel tanks and air-conditioning systems, for efficiency and proper safety to be observed. Thus, it makes use of a Vacuum Leakage tester to test a possible leak from a fuel tank or an engine system that may cause performance problems or safety issues.
Food and Beverage Industry
A vacuum test machine aims to tighter seal on food packaging to ensure that the food remains fresh and contamination-free.
Example – Vacuum sealing canned goods, beverages, and pre-packed snacks in the food and beverage sectors to remain fresh. A vacuum leak testing equipment will check if there is an airtight seal that would prevent spoilage or contamination from occurring.
Benefits of Vacuum Leakage Tester

Non-Destructive Testing: The non-destructive testing is the biggest benefit of the vacuum leak testing method. It does not damage the product under test. That is important in high-value or sensitive products where they are not compromised for any reason during their inspection.
Detect Minor Leaks: Among the highest benefits obtained through vacuum leak testing equipment is that they can detect even the smallest leaks, which may otherwise be unnoticed. It gives no room for poor-quality products, and its sensitivity ensures that high-quality products reach the highest quality standards.
Quick and Efficient: The vacuum leak test apparatus is an extremely fast test process. Fast detection of leaks through tests helps to achieve nearly instantaneous results, and this also helps keep the lines of production running without significant delays, which is quite ideal for heavy manufacturing processes.
High-quality Products: Vacuum leak testing ensures that the products are sealed correctly. A reliable seal is typically airtight and provides better quality and performance over time. Such consistent quality contributes to gaining the trust and loyalty of customers, which is considered extremely important for the maintenance of a strong position in the market.
Highly Adaptable: Vacuum leak testing machines are very flexible and can be very applicable in different industries. Whether in packaging, electronics, automobile, or aerospace, the flexibility to check for leaks across all these products puts the vacuum leak tester at the center of this versatility of applications.
Enhanced Brand Reputation: There is a high probability of reliable performance of a product for the lifetime leak-free. Vacuum leak testing will ensure that all seals are good, with no failures from undetected leaks. Overall, this increases product reliability, minimizing the chances of its failure to function or break down, hence giving the customer a product that meets the expectations.
Improved Customer Trust: Trust in products comes from regular dependability that ensures quality and reliability are at acceptable levels, hence increasing confidence in the brand. If customers are assured that their products are leak-free and meet the expected quality standards, there is increased confidence in the brand; they will also order again and again from it.
Why Should You Choose Testronix Vacuum Leak Tester

Testronix is a leading lab testing equipment that offers high-precision and high-standard vacuum leak testers. With its efficient leak detection equipment, industries can ensure product integrity, safety, and performance. It is an ideal choice for industries including packaging, pharmaceuticals, food and beverage, automotive, and electronics Due to its cost-effective solutions, industries all over the world frequently use vacuum test equipment offered by them. Here are some detailed benefits –
Highly Sensitive and Precise – Testronix Vacuum Leakage tester is designed to be sensitive and precise enough for even minute leak detection. This simply means that even the smallest leaks will be found, so products are sure to be fully inspected to meet the highest quality tests that avoid problems that could affect both usability and safety.
Durability and Reliability – A tough build makes the Testronix Leak tester ideal for production in high volumes, but they come with robust builds; high-quality materials ensure long life with minimal maintenance requirements.
Versatile Application – Our vacuum leak test apparatus is highly versatile and easy to adapt over the industries. It can be applied to a wide range of products, which vary from sealed food packages to critical medical devices and automotive components. This broad capability makes our vacuum leak test machine perfectly suitable for businesses that have diverse testing needs for different products and materials.
User-friendly with Advanced Features – Testronix machines are user-friendly, so even the most non-technical member can easily work on a machine. Advanced features like settings of adjustable vacuums, customizable test times, and display capabilities make test operations very efficient. Each test is controlled and monitored to the best extent possible.
Cost-effective Yet Efficient – With our cost-effective leak tester, we minimize waste, the cost of recalls, and manage a better production process. These testers are fast, and reliable, and cut down on costs considerably; therefore, wastage of product, repair, or replacement due to a defective product is reduced significantly.
Highly Standardized Tester – Our testers are designed to test according to industry-standard testing methodologies, such as ASTM and ISO standards to make your products compliant with regulatory requirements. Choose Testronix to guarantee compliance with international standards and meet the quality expectations of global markets.