Maintaining wall thickness in materials, in products such as plastic containers, metal pipes, automotive parts, and packaging materials, is among the most fundamental issues in quality control. The structural integrity and durability of a product are greatly influenced by wall thickness.
Whether it's the strength of the pipeline, the plastic casing, or a metal component, variations in thickness may cause product failure, generate waste material, or even danger. For manufacturers, the right wall thickness can ensure precision, quality of product, cost efficiency, and compliance with relevant legislation. That is when gauges for wall thickness become important.
What are wall thickness gauges?
Wall thickness gauges are highly advanced instruments able to measure the thickness of materials such as plastic, metal, and composite materials without damaging them. The most basic requirement is that it should ensure that a product is based on the indicated quality standards, there are various types of wall thickness gauges depending on the type of material, and certain conditions for measurement such as:
- Ultrasonic Thickness Gauges
- Eddy Current Thickness Gauges
- X-ray or Gamma Ray Thickness Gauges
- Mechanical Dial Gauges
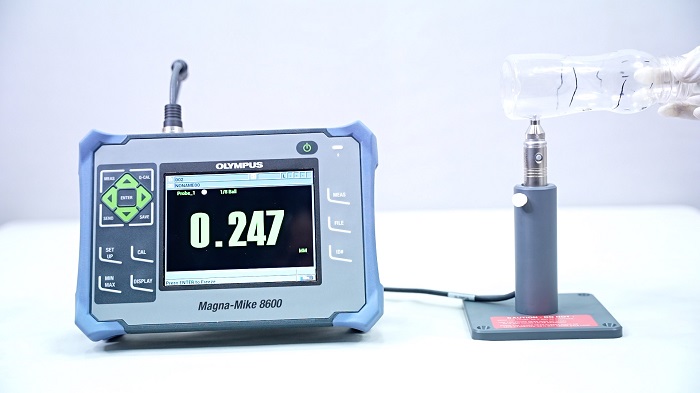
Each of them is utilized for a specific purpose in the process to correctly, uniformly, and according to standard measure the thickness of the wall of the product.
Why Testronix?
With years of experience and technological know-how, Testronix has been the ultimate business partner to companies for reliable and precise quality control instruments. From a diversified list of clients, Testronix has always delivered the precision and reliability global brands demand.
Testronix’s brand tradition of quality instruments has reached the mark of user-friendliness and high accuracy. Their wall thickness gauges are trusted for ensuring international standards, manufacturing process improvement, and improved quality of products.
Role of Wall Thickness Gauges in Quality Control
Wall thickness gauges have a very important role to play in the quality control arena, ensuring that products meet specifications and performance criteria. There are the following roles that wall thickness gauges perform:
1. Maintaining Uniformity and Conformance:
- The keyword for manufacturing is consistency. Wall thickness gauges ensure that the product produced every moment falls within the specified range of thickness. In many industries, such as aerospace, automobile, and packaging, the regulation for the material thickness of the product for safety and performance is very strict.
- Having accurate measurements and real-time wall thickness gauges enables manufacturers to strictly adhere to the set standard by ISO 9001, ASTM, and industry-specific norms.
- Such uniformity in the wall thickness can stop costly and expensive defects, increase the reliability of products, and allow all the products to function as expected under actual service conditions.
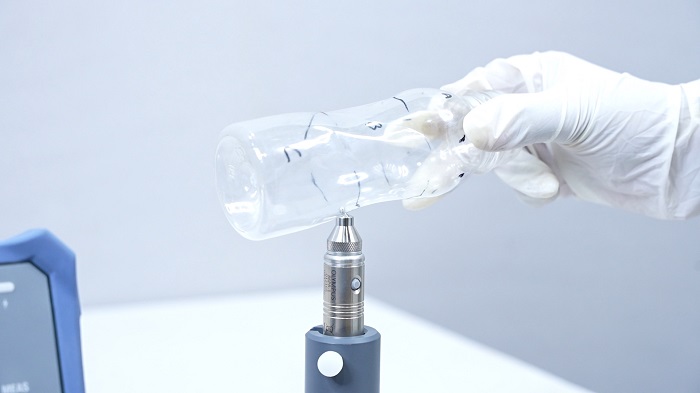
2. Elimination of Waste Material and Reducing the Production Cost
- One of the significant advantages of wall thickness gauges is that they can help manufacturers manufacture at minimum material waste. In a product where the thickness is too much, manufacturers then consume more material than needed, and as such, the production cost is increased. If the thickness is too low, then the product may lack the strength needed, which often leads to failures and pricey recalls.
- Wall thickness gauges allow the right thickness all through manufacture. This translates to efficient manufacturing procedures and sound cost control, together with the quality, strength, and durability of the end product.
3. Structural weaknesses and defects
- Many products in numerous industry fields are prone to structural weaknesses due to slight deviations in wall thickness. For instance, in the automotive industry, irregular deviations in the wall thickness of parts like engine parts or fuel tanks may lead to failure due to stress for a given level of safety and reliability.
- Such wall thickness variations in oil and gas pipelines become vulnerable weak points with a high potential for leakage or breakage resulting in environmental damage or expensive repair. It is possible to detect such weaknesses at an early stage of the manufacturing process by monitoring the product through regular use of wall thickness gauges along the line.
4. Increase in Product Resistance and Safety
- There are also wall thicknesses that really control material properties on the basis of safety and durability, as in the case of products manufactured in the construction industry. Wall thickness in steel beams and pipes can compromise building and infrastructure integrity if inconsistent.
- Similarly, in the packaging industry, the strength and durability of packaged materials are strictly dependent on wall thickness. That is to say, by manufacturing packaging products like bottles, cans, or containers with uniform wall thickness, producers can avoid breakages or spoilage of the product and thus enhance both product performance and safety.
5. Improving Efficiency in Operations
- Wall thickness gauges also enhance efficiency during operation by making quality control operations easier. Since these gauges directly provide information relating to the wall thickness on output, identifying defects becomes much easier and corrections can immediately be made.
- This renders much lower incidences of downtime and less material wasted, along with increased productivity and improved overall flow of production.
FAQs
What types of industries can apply wall thickness gauges?
It is broadly used in ventures like packaging, auto, aviation, development, oil, gas, etc
What is the working principle of an ultrasonic wall thickness gauge?
They work based on the principle of using high sound frequencies for the measurement of material thickness. It calculates the thickness by considering the time of travel undertaken by the sound wave. Later, the rebound time is considered to arrive at the determination of the thickness of the material. This technique can also be used for non-metals as well as metals.
Why is wall thickness measurement important in packaging materials?
Consistency in wall thickness for bottles and containers of packaging materials would, therefore, ensure the product is fairly adequate to protect contents without using more than materials that are not yet required for such protection. It also reduces breakage and ensures that the package meets safety and regulatory standards.
Phone: +91 9313 140 140
Email: info@testronixinstruments.com