Imagine a carbonated soft drink bottle bursting on the shipment or a supermarket shelf. Such an event does not only bring losses to the product but also impacts the brand image and consumer safety. Therefore, there is an excellent and critical demand for durable PET bottles which could face pressure under numerous conditions. The Bottle Burst Test appears as the most serious solution, making a fair and approximate calculation possible concerning the toughness and strength of PET bottles. Highly implemented in industries concerning beverages, drugs, and cosmetics, they aim at assurance to quality safety satisfaction in its clients.
Bottle Burst Test: What is it?
The Bottle Burst Test checks whether a bottle can withstand internal pressure without breaking. It replicates conditions under which the pressure inside the bottle increases, making sure that it can withstand carbonation or temperature stress. In the case of PET, glass, or plastic bottles, this test applies controlled pressure to identify weaknesses or structural flaws that may lead to failure. This is done in advance to ensure product quality and customer safety.
Why is the Bottle Burst Test Important in PET Packaging?
- Safety: Avoids accidents from bottle explosions resulting from internal pressure.
- Quality Assurance: Satisfies industry standards and regulatory norms.
- Customer Satisfaction: Product integrity is preserved during transportation and storage.
- Cost Efficiency: Saves on waste, product recalls, and financial losses due to damaged goods.
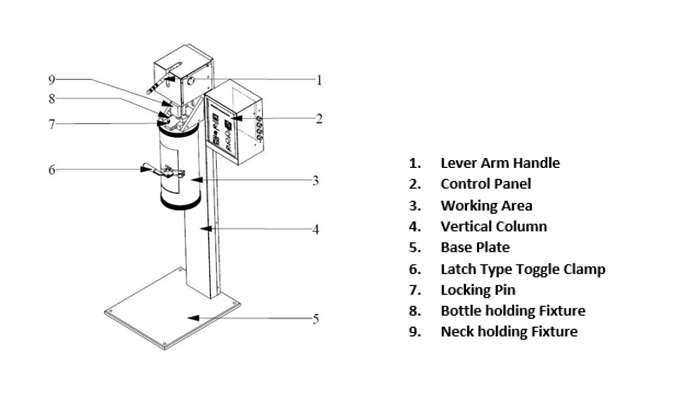
How is the Bottle Burst Test Carried Out?
The test procedure includes:
Preparation of the Test Bottle
- Sample Selection: A sample bottle (PET, glass, or other pressurized containers) is chosen for testing.
- Labeling: Each bottle is labeled for accurate identification during the test.
-
Filling the Bottle
- Water or Air Filling: Water or air is used to simulate the pressure the bottle would experience in real life. Water is used for carbonated beverages, while air is used for other purposes.
- Sealing: The bottle is tightly sealed to prevent leakage during the test.
-
Setting up Testing Apparatus
- Bottle Burst Tester Setup: The bottle is placed in the Bottle Burst Tester, which has a chamber for applying internal pressure.
- Pressure Regulator and Timer: This sets the pressure, while a timer records how long the test lasts.
-
Application of Internal Pressure
- Gradual Pressure Application: Pressure is applied gradually, with the tester ensuring controlled build-up inside the bottle.
- Pressure Monitoring: The calibrated pressure gauge continuously monitors the internal pressure, ensuring it falls within the test range (e.g., 6 to 8 bars for PET bottles).
-
Testing the Bursting Point
- Pressure Build-up: Pressure is increased gradually to assess the bottle’s resistance up to its capacity.
- Observation: If the bottle withstands the pressure, it will show no deformation. If it bursts, the pressure at failure is recorded.
-
Result/Variation Check
- Alarm Trigger: When the bottle bursts, the alarm signals the end of the test. If the bottle withstands the pressure, it passes.
- Recording Data: Burst pressure, time to failure, and other relevant data are recorded for analysis to determine the bottle’s suitability.
-
Final Evaluation
- Evaluation of Results: The bottle's burst strength is assessed based on the recorded data. If the bottle meets the pressure requirements without failure, it is deemed suitable for holding pressurized liquids.
- Inspection for Weak Points: Any cracks, leaks, or deformities before the burst are noted as potential weaknesses in the design or material.
-
Important Considerations
- Calibration of Pressure Gauge: The pressure gauge and timer are calibrated to international standards such as ASTM C 147-86, verified by accredited calibration labs like ISO/IEC 17025.
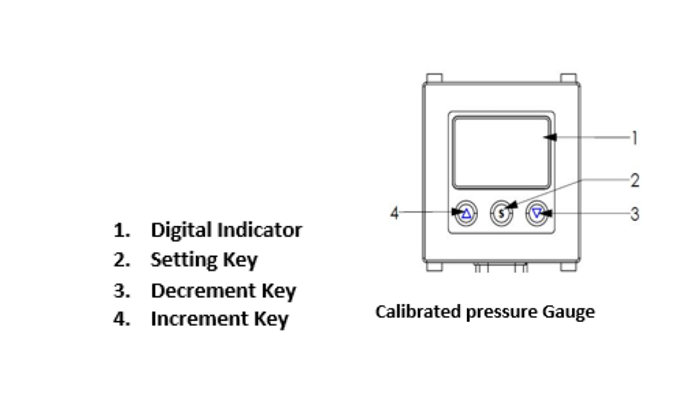
-
- Material-Dependent Testing: PET, glass, and plastic bottles have varying pressure tolerance. PET bottles typically withstand 2.5 to 5 bars, while glass bottles may handle 4 to 6 bars (or 6 to 7 bars for reinforced bottles).
- Test Specifications: The test follows international standards such as ASTM, ensuring accurate, repeatable results.
The Objective of the Bottle Burst Test
The test is aimed at determining whether a bottle can withstand internal pressure without bursting. For instance, PET bottles containing carbonated drinks should be able to resist high pressure over an extended period. Bottles that fail this test are not safe for applications where they will be subjected to pressure.
Important Features of Bottle Burst Tester
- Testing Parameters: The pressure regulator allows users to set the desired test pressure and time. The test applies a maximum of 260 psi, which is enough to analyze bursting strength.
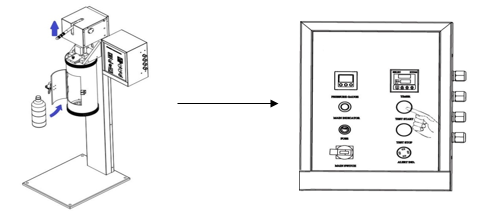
- Testing Process: The bottle bulges under pressure, and if it fails to sustain it, the bottle bursts. The system alerts the user with an alarm upon test completion.
- Calibrated Pressure Gauge: The pressure gauge and timer ensure proper simulation of internal pressure. The NABL certification for Testronix calibration ensures precision and is therefore compliant with ISO/IEC 17025.
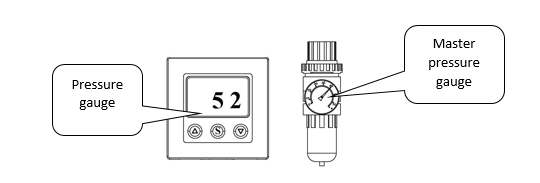
- Compliance with Standards: It conforms to ASTM C147-86, which sets the methods of testing the bottles' internal pressure strength.
Minimum Pressure Requirements for Bottles
1. PET Bottles:
Carbonated Beverages: 2.5–5 bar (36–73 psi), Burst pressure: 6–8 bar (87–116 psi).
High-strength PET Bottles: 4–6 bar (58–87 psi).
2. Glass Bottles:
Standard Bottles: 4–5 bar (58–73 psi).
Reinforced Bottles: 6–7 bar (87–102 psi), Burst pressure: 8–12 bar (116–174 psi).
FAQs
What types of bottles can be tested by the Bottle Burst Tester?
The tester can be used with PET, glass, and plastic bottles that have applications in relation to beverages, pharmaceutical applications, or any application that requires resistance to pressure.
What is the maximum pressure that can be applied on the Bottle Burst Tester?
Testronix Bottle Burst Tester can deliver as much as 260 psi. It's so much more than any bottle requires that full strength can almost certainly be confirmed.
Why is a calibrated pressure gauge necessary in burst testing?
A calibrated pressure gauge ensures accurate simulation of pressure conditions, providing precise and reliable test results in compliance with international standards.